The different processes in the area of fibre composite technology
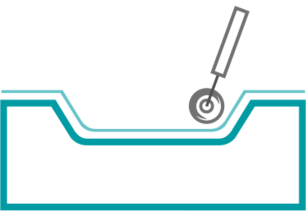
HAND LAMINATION
In this process, glass-fibre mats are cured in the moulds via manual impregnation with polyester resins (UP resins). Particularly high strength can be achieved via this method. Curing usually takes place at room temperature. This process is mainly used for smaller series and larger component geometries, as well as for mould making and prototypes of all kinds.
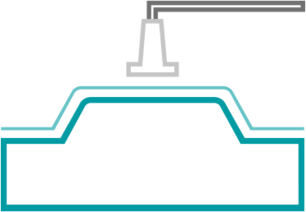
VACUUM INFUSION
In this process, layers of dry glass-fibre scrims are draped in a single-shell mould. In the next step, the mould is sealed with a vacuum bag. Liquid resin, usually epoxy resin (EP resin), is injected into the mould under vacuum.
FOAMING
In the foaming process, glass-fibre mats are soaked in a foam resin inside a mould cavity. After the two-part mould is closed, the foam is able to expand and is thus formed into the desired shape. Foaming technology is used if a low-density product is desired.